Researchers Make Complex 3-D Surfaces with 2-D sheets
Researchers have developed a way to create flat sheets of a rubbery material that expand into three-dimensional geometries, such as a human face, when exposed to heat.
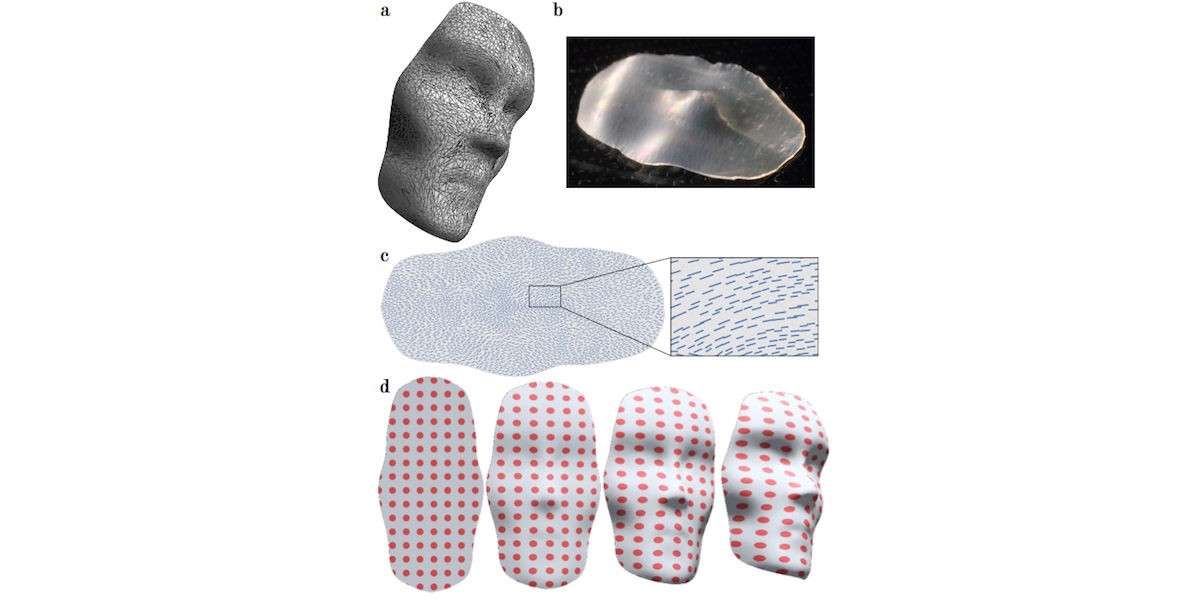
Jiffy pop, an aluminum foil pan full of popcorn kernels and oil, is a staple of camping trips. Because of the way the pan is designed, when placed above an open campfire the kernels expand the aluminum top as they heat and pop, ultimately resulting in a bag of popcorn. The aluminum is lined with ridges, which unwind, allowing it to expand into a spherical shape.
Now, researchers at the University of Pennsylvania have used a similar concept to design two-dimensional sheets of a rubber-like material called liquid crystal elastomer capable of transforming into complex three-dimensional geometries, such as a human face, with heat. This has countless technological applications in areas such as flexible electronics, metamaterials, aerospace, medical devices, and drug delivery.
The research, done by Hillel Aharoni and Randall Kamien of the School of Arts and Sciences and Yu Xia, Xinyue Zhang, and Shu Yang of the School of Engineering and Applied Science, has been published in the Proceedings of the National Academy of Sciences.
“The main idea,” says Kamien, “is suppose that instead of blowing it up by inflating popcorn beneath it, we designed it so that the material stretched out along those ridges all by itself. We created a material with little artificial muscles that, all by themselves, pull it open into preprogrammed shapes when heated.”
The researchers started with flat sheets of liquid crystal elastomer, which deform a certain way when heated. Aharoni had the idea of taking this material and programming it with certain shapes so that they could control how the material deforms. He struck up a collaboration with Xia, who was able to demonstrate Aharoni’s theories through experiments.
The process has a similar function as 3-D printing, but with the benefit of being less expensive and time consuming. One can start with a 2-D sheet or film and turn it into any 3-D geometry desired simply by applying heat, light, or other stimuli.
Initially, the researchers were able to program the sheets to create more simple geometries like spheres and leaves. The challenge to designing a replica of a human face is that it has curvatures that go in and out, for instance the bridge of a nose. Designing a material with dents and bumps is much more difficult as the material could pop in rather than popping out, ruining the design of the face.
“The initial goal was to look at how to design more challenging geometries,” Yang says. “We wanted to know exactly how to control the shape. The face is a perfect example because it has many different curvatures. In the case of a sphere or leaf, it doesn’t matter which direction the material indents because you can flip it and get same structure. This isn’t possible with a face.”
Xia was able to design the material so that the top stretched a certain way and the bottom stretched in almost the same way, with subtle differences. These small adjustments to the top and bottom of the sample tell the material which way to curve, allowing for greater control of the final shape.
“The advantage of this procedure,” Aharoni says, “is that you can have large deformations one way and you can start accessing shapes that have features that are much smaller in scale, which you can start to control.”
One of the most valuable things to come out of the research, says Aharoni, is the collaboration between theorists and experimentalists.
“The fact that we got to collaborate and have this back and forth,” Aharoni says, “gave us results that might not have been possible if it was just a theoretician publishing a paper and then an experimentalist trying to work on it separately. If something didn’t work we could work together to figure out new ways of doing it.”
A potential application of this research is in treating burns and scars. Often when people get burns, they are treated by using covers with particular shapes that help the skin heal. Being able to precisely control the shape of the material could allow for customized therapeutics, programmed to the shape of the individual.
In addition to seeking out more potential applications, the researchers hope to continue to work on the method to optimize it and tackle other limitations from both the theoretical and experimental sides. One thing they hope to figure out is how to program a sequence of shapes to allow the material to have different functions.
“The exciting things,” Xia says, “are both the range of possibilities and the fact that everything is very applicable. It’s not some abstract theory. This research holds huge possibilities for the future. It will enable us to do things that we could only imagine before.”
Hillel Aharoni is a postdoctoral fellow in the Department of Physics and Astronomy in the School of Arts and Sciences.
Randall Kamien is a Vicki and William Abrams Professor in the Natural Sciences in the Department of Physics and Astronomy in the School of Arts and Sciences.
Yu Xia is a postdoctoral fellow in the School of Engineering and Applied Science.
Shu Yang is a professor the in the Departments of Materials Science and Engineering and Chemical and Biomolecular Engineering in the School of Engineering and Applied Science.
This research was supported by the National Science Foundation.