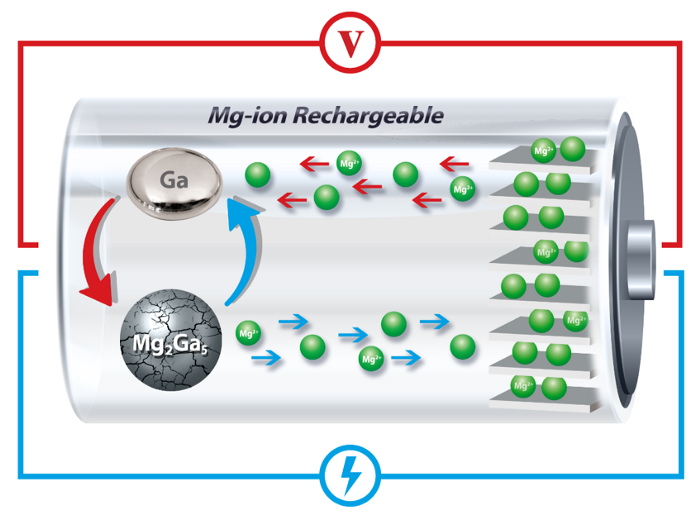
Rechargeable lithium-ion (Li-ion) batteries are a revolutionary technology, found in everything from cellphones to cars. Their ubiquity and role in breaking dependence on fossil fuels earned a trio of researchers this year’s Nobel Prize in Chemistry.
But even as Li-ion battery technology is being recognized with one of science’s top prizes, the chemistry behind them is facing a looming challenge. Lithium-ion batteries cannot be recharged indefinitely; the materials in these batteries’ electrodes expand and crack with each cycle, gradually decreasing their storage performance until they are useless. The resulting demand for fresh lithium, cobalt and other necessary elements puts a strain on natural resources.
With this challenge in mind, Penn Engineers are looking to design rechargeable battery electrodes that can work efficiently with metal ions other than lithium. Magnesium-ion batteries are a promising alternative, but materials that can reversibly store magnesium have thus far been even more susceptible to the cracking and other problems than their Li-ion cousins.
The Penn researchers have now found a solution by incorporating gallium, a metal that has a melting point a few degrees higher than room temperature, into the anode of a magnesium-ion battery. By melting and solidifying with each charging and discharging cycle, these anodes can “heal” the cracking and subsequent expansion that normally degrade rechargeable battery storage.
Their experiments show that this new anode significantly extends the life of magnesium-ion batteries, and does so without the need of expensive nanoscale materials. These traits could make magnesium-ion batteries a good fit for large-scale applications, taking pressure off lithium resources.
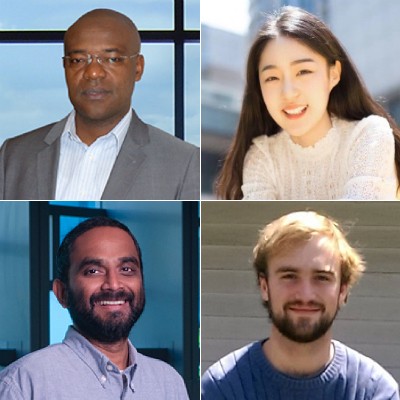
The researchers demonstrated their gallium-based anode in a study published in Advanced Energy Materials.
The study was led by Eric Detsi, Stephenson Term Assistant Professor in the Department of Materials Science and Engineering, along with Lin Wang and Samuel Welborn, graduate students in his lab. They collaborated with Vivek Shenoy, Eduardo D. Glandt President’s Distinguished Professor in the Department of Materials Science and Engineering.
“For most electric vehicles, the weight of the battery represents about a fifth of the vehicle’s overall weight. Relying solely on lithium-ion batteries to power these vehicles around the world will put considerable strain on lithium and cobalt resources used in the batteries,” Detsi says. “They are already becoming more expensive due to demand, and the global cobalt market heavily depends on supplies from countries with high geopolitical risks.”
“It is obvious that alternative battery technologies are needed,” he says. “Not to replace lithium, but to support lithium.”
Charging and discharging a battery involves chemical reactions that allow ions to move from one electrode of the battery to the other, gaining or releasing electrons in the process. However, anyone with an aging cellphone or laptop knows that these batteries lose their ability to hold a charge over time. One of the main reasons that these batteries fail is that the charging-and-discharging cycle involves a physical transformation of the materials in the electrodes. When ions are incorporated into the electrode, those materials expand, and when the ions are released from the electrode, the materials crack. This process continues until the materials break and physically lose electrical contact with the electrodes, making the battery unusable.
“The volume change that occurs in most electrode materials due to incorporation and release of ions leads to cracking and pulverization. It’s one of the things that kill a battery,” says Wang. “This pulverization is associated with the stress buildup that comes with a solid-solid phase transformation.”
“In our new work, however,” Welborn says, “instead of a transformation from one type of solid into another, the original solid material transforms into a liquid. This inhibits the cracking and pulverization because the stresses associated with the normal solid-solid transformation are no longer present.”
At room temperature, pure gallium is a malleable, silvery metal that could easily be mistaken for aluminum or nickel. Holding some in your hand, however, quickly reveals a unique property: with a melting point of 85 degrees Fahrenheit, body temperature is enough to turn a solid piece of gallium into a mercury-like liquid.
In the researchers’ new study, the gallium starts out in a solid form because it’s alloyed with magnesium in micron-sized particles.
“In order to electronically connect these small pieces,” Wang says, “we put them into a conductive network of carbon fibers, carbon black and graphene which is all tied together with a binder.”
When the magnesium ions separate from the gallium, it transforms into its liquid state because the battery operates at temperatures slightly above gallium’s melting point.
“Since it’s bundled up in this network of other materials,” Welborn says, “when the gallium goes from solid to liquid, it does not move around like you might expect a liquid to do.”
Using X-rays to examine the crystal structure of the materials inside the battery, the researchers showed that when the battery charges, ions return to the anode and re-form solid gallium-magnesium particles.
Critically, since these particles are reconstituted with each cycle, they don’t experience the kind of cracking that eventually degrades other batteries.
The researchers’ experimental battery withstood more than a thousand charging cycles, approximately five times more than the current state-of-the-art magnesium-ion battery.
“The thousand cycles demonstrated in this work represents a significant improvement,” Detsi says, “but our dream is to take advantage of this unique self-healing behavior to design a battery that can be charged and discharged forever.”
The limit on the new battery’s thousand-cycle lifespan is not due to the electrode, but rather the electrolyte, the liquid medium that moves ions from one electrode to another. Earlier research from Detsi’s group has shown the role the electrolyte plays in slowly degrading the battery electrodes, and future work will focus on how to ameliorate that process.
Fortunately, as with the design of the study’s self-healing electrodes, working on this aspect of battery design involves clever applications of chemistry, rather than cost-prohibitive nanotechnology techniques other attempts at extending battery life entail.
“To fix the issues with lithium-ion batteries, the battery community commonly uses nanomaterials,” Detsi says. “However, the synthesis of nanomaterials can be complex, meaning that making tons of nanomaterials at an industrial scale for battery applications can be very expensive. One remarkable thing with our design is that there is no need to use nanomaterials, which makes this class of batteries very attractive for large-scale applications.”
Also contributing to the study were Manni Li and Zeyu Wang, graduate students in Detsi’s lab, and Hemant Kumar, a postdoctoral researcher in Shenoy’s lab.
The research was principally supported by the Vagelos Institute for Energy Science and Technology (VIEST) through a 2018 VIEST seed grant, the National Science Foundation (NSF) through NSF EAGER grant CMMI-1840672 and NSF MRI grant 17–25969.