Thanks to technologies like 3D printing, shapes and structures that would have been arduous or impossible to make a decade ago can be fabricated almost as fast as they can be designed on a computer. For engineers, the transition from digital to physical has a major obstacle, however: The materials that can be processed by 3D printers are rarely the ones that engineers want to use in finished products.
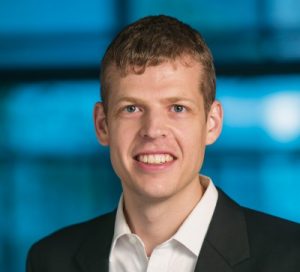
Jordan Raney, who joined Penn Engineering in the fall of 2016 as an assistant professor in Mechanical Engineering and Applied Mechanics (MEAM), thinks there is a way to get the best of both worlds.
“3D printing has been of explosive interest in recent years because of the exciting structural features that can be designed, which can result in new and useful properties,” Raney says. “Yet the majority of commercial 3D printers require the use of materials, such as thermoplastics and photopolymers, that are of limited utility in many applications of interest to engineers, notably structural applications. This has tended to limit the use of 3D printers to modeling and prototyping rather than manufacturing.”
Working at the intersection of mechanical engineering, physics, materials science and nanoscience, Raney is developing new engineering materials by controlling their structure at multiple length scales simultaneously. He envisions a world where 3D printers could manufacture structures on an industrial scale, while making microscopic location-by-location adjustments to their composition, as determined to be most efficient for the mechanical loading they will experience.
Reimagining Materials
During most of human civilization, engineers were limited to the as-is materials provided by nature: things, like stone, wood and metals. Until very recently, their properties and inherent strengths and weaknesses could only be gently influenced, not radically changed. However, advances in materials synthesis and fabrication techniques, through disciplines such as polymer science and now nanoscience, mean that all bets are off when it comes to a material’s properties.
Materials research today spans not only the study of the known properties of materials, but the discovery, development and “programming” of new materials at the molecular level. This means making use of approaches such as self-assembly, where engineers design nanoparticles such that physical and chemical forces cause them to combine into complex structures. To exert more control over a large range of length scales simultaneously, Raney seeks to combine these techniques with 3D printing.
Existing 3D printing materials are used because their properties are compatible with the way the printers work. The plastic commonly used in consumer-grade printers, for example, is made to quickly melt enough to be extruded through a moving nozzle, then harden, layer-by-layer, into the object being printed. The qualities that enable objects to be fabricated this way also make those objects unfit for many applications.
Raney’s group is interested in designing materials that use more chemically complicated processes than melting and cooling. By suspending nanoparticles in a malleable paste and controlling their orientation as they’re extruded, they aim to design the internal structure of an object as carefully as they build its overall shape. These objects would be tougher, stronger, or stiffer but also lower weight than what can be made by existing means — a constant demand in the aerospace and transportation industries.
“It is an important goal of our group to be able to make these complicated features out of materials that are relevant to engineers, so we study both structural mechanics — what should our structure look like — and materials — what materials should our structures consist of,” Raney says. “For example, if we can come up with a complicated structural design that allows engineers to completely control how vibrational energy moves through their new aircraft fuselage, but we’re doing so by using a polymer that will break down during operation, we’re not solving the problem.”
An added boon to this approach is that through controlling the internal structural features, the group can also develop entirely new properties that don’t exist in traditional materials, such as controlling how and where energy propagates through a material during an impact. Such materials could even be “programmable” — exhibiting highly tunable mechanical responses depending on defined inputs, such as humidity, voltage or impact during its operations.
“In recent work,” Raney says, “we have explored the control of local fiber alignment in 3D-printed composites. Using these approaches, one can 3D print two structures with identical mass, composition, and geometries but with vastly different mechanical responses based on the manufacturer’s choice of microstructural features.”
Coming to Penn
Following the completion of his doctoral degree in Materials Science at the California Institute of Technology in 2012, Raney was a postdoctoral fellow in the Wyss Institute for Biologically Inspired Engineering and the John A. Paulson School of Engineering and Applied Sciences at Harvard University. There, he worked in the laboratory of Jennifer Lewis, Hansjorg Wyss Professor of Biologically Inspired Engineering, where his research focused on the mechanics and fabrication of novel material architectures, including hierarchical, heterogeneous, fibrous and soft systems.
Now at Penn, Raney looks forward to increased opportunities for collaboration. “What drew me to Penn was its rare combination of a relatively small-size engineering school and its widespread university-level excellence,” he says. “With my research as interdisciplinary as it is, it could very well be that five years from now I will be working with individuals in some department at Penn that I never would have guessed I’d have cause to interact with. The fact that Penn is excellent in the fundamental sciences, medicine, business and engineering, and is willing to make large, enabling investments in infrastructure, such as the Singh Center for Nanotechnology, makes it a fantastic place to be.”
“Jordan’s research is a terrific addition to MEAM, and I’m excited about what his group will be producing in the coming years,” says Robert Carpick, John Henry Towne Professor and chair of MEAM. “His activities are highly interdisciplinary, and we’re imagining he’ll be quickly forming collaborations across Penn and beyond.”
In addition to his research aims, teaching forms an important part of Raney’s excitement about being at the University. “Student quality is one of the many things that drew me to Penn. It is easy to make the mistake of quickly glossing over technical problems when you’ve seen them many times previously,” he says. “But as you present such a problem in a classroom, the questions that the students ask force you to reengage with the material in a new way. That is a very rewarding thing, and it reminds you that we’re all students.”
Raney’s near-term research goals are to produce 3D-printable engineering materials with better strength and fracture toughness by improving control of microstructural features inside the material that is being printed rather than changing its overall shape. He also envisions the marriage of stimuli-responsive materials to complex nonlinear structures, especially in the context of soft materials commonly used in robotics and therapeutic devices.
Ironically, Raney’s long-term research goals involve using natural materials for design inspiration.
“If you look at natural materials like wood or bone you see incredibly complex microstructures,” he says. “In exploring their mechanical behaviors, you find that these complicated microstructures are in fact very well-optimized, producing macroscopic mechanical properties that are very efficient at being as stiff, strong, and as tough as possible for as little weight as possible. When you compare this picture with our synthetic materials, it’s a bit embarrassing.”
In spite of burgeoning scientific advances, Raney acknowledges that we still lack the fabrication tools necessary to vary the microstructure in nature’s subtle ways. But even if we possessed these tools, theory hasn’t advanced enough to guide them; we don’t yet know what microscale structural features belong where.
“In my ideal, long-term, science-fiction vision,” Raney says, “we would be able to define some engineering scenario — say an aircraft wing subjected to defined aerodynamic forces — and then automatically generate the ideal multiscale, heterogeneous microstructure throughout the entire wing, with both the right structure and the right composition, varying from location to location as forces vary — -and then fabricate it as one large 3D-printed structure. We have rather a long way to go.”