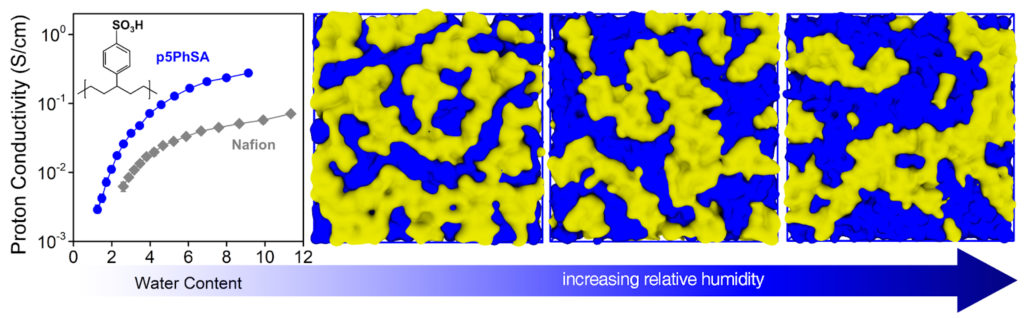
Fuel cells are likely to become an important energy conversion solution, as they can turn clean, abundant hydrogen into large amounts of electrical power — enough for a vehicle or to serve as emergency reserves for a house — without producing carbon emissions.
The chemistry that releases the energy from hydrogen is relatively simple, but the materials necessary to keep this reaction going at useful scales are anything but. A fuel cell’s electrolyte, for example, determines how quickly the cell’s fuel is converted into energy, but is also responsible for insulating the electrodes from one another. Materials that can achieve rapid proton conductivity while blocking electrons in the harsh environment of fuel cells typically contain fluorine, which increases their cost and environmental impact.
Now, an interdisciplinary team of researchers from the University of Pennsylvania’s School of Engineering and Applied Science, Sandia National Laboratories and Florida State University has designed a new electrolyte material that solves some of these problems.
The key to their findings, recently published in the journal Chemistry of Materials, was precise control over the placement of sulfonate groups on a polymer. When fabricated into thin films and infused with water, these groups find each other and form wide and interconnected channels for protons to flow through.
Proton conductivity tests of their new polymer electrolyte showed it performed four times better than the current industry standard. Better still, the polymerization method used to make the researchers’ polymer is one already in commercial use, smoothing the path to transitioning this new material from lab to production for use as a fuel cell electrolyte.
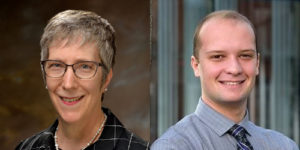
The study was led by Penn Engineering’s Karen I. Winey, Harold Pender Professor in both the Departments of Materials Science and Engineering and Chemical and Biomolecular Engineering, and graduate student Benjamin A. Paren, along with Amalie L. Frischknecht, Mark J. Stevens and Bryce Thurston of the Center for Integrated Nanotechnologies at Sandia National Laboratories, and Justin Kennemur of Florida State University.
In the fuel cell industry, a solid polymer electrolyte known as Nafion is the state of the art, but finding a replacement for it is highly desirable, as Nafion’s fluorine-based chemistry requires a difficult and thus expensive synthesis process.
The development of novel materials can be unpredictable, however, as they don’t always have the properties their molecular structures would suggest. Polymers, the kind of materials Winey and her colleagues specialize in, have an additional layer of complexity when the polymer contains functional groups, in this case acid groups. The functional groups in many polymer electrolytes are randomly scattered along the polymer chain, but here the acid groups are precisely located on every fifth backbone atom. This consistency leads to exceptionally well-defined nanoscale structures that improve the electrolyte’s performance.
“In a previous strategy we worked with polymers that form planar pathways for the protons to travel through,” Winey says. “To achieve excellent conductivity across the entire material would require aligning the planar pathways to avoid having paths that don’t line up exactly with adjacent, thus making a bunch of dead ends. Having regions of the electrolyte where protons can move very fast is useless if there are also regions where they get stuck.”
The researchers’ new strategy meant finding a polymer that would first assemble into fully connected paths, then expanding those paths such that the average conductivity would be the same in all regions of the electrolyte.
Winey had an idea for the structure of such a polymer from previous work, but successfully putting it together required particularly difficult chemistry. Winey had previously collaborated with Frischknecht and Stevens, who have used molecular dynamics simulation to reveal the nanoscale assemble of the functional groups. Kennemur introduced himself to Winey as having a strong interest in precision polymer synthesis using a particular chemistry technique, known as ROMP, that could actually synthesize the polymer in question.
“Amalie has been working on polymer electrolyte simulations for more than a decade, and Justin was interested in ROMP, just thinking up new things to make,” says Winey. “None of us could have done this on our own.”
ROMP, or ring-opening metathesis polymerization, allows for the acid-containing “pendants” to be attached along the polymer’s backbone in an equidistant fashion. The researchers’ simulations showed that when the sulfonic acid groups are located at regular intervals, they self-assemble into aggregates that produce channels that connect across the material. And because these groups are attracted to water, these channels can be expanded simply by exposing the polymer to humidity.
The researchers’ experiments then showed a direct relationship between the amount of hydration supplied and the proton conductivity of the resulting polymer.
“At its peak, the proton conductivity was equivalent to the conductivity in pure water,” Winey says. “It’s as if the protons don’t see the polymer at all, though it will still do its job as an electrical barrier between the electrodes.”
The next steps include improving the mechanical toughness of the polymer and evaluating the electrochemical stability of this fluorine-free polymer electrolyte.
“New materials usually have a very long runway,” Winey says. “What’s nice about this one is that because ROMP is practiced commercially, you’re starting halfway down.”
Penn Engineering undergraduate student and Winey group member Arjun Kanthawar, along with William J. Neary and Aaron Kendrick of Florida State University and Manuel Maréchal of Université Grenoble Alpes, also contributed to the study.
The research was supported by the National Science Foundation through grants DMR 1904767, PIRE 1545884, and CBET 1804871, Penn’s Vagelos Institute for Energy Science and Technology through a graduate fellowship, the Agence Nationale de la Recherche through grants ANR-15-PIRE-0001-01 and ANR-15-PIRE-0001-04, and the Florida State University Energy and Materials Hiring Initiative. This work was also performed, in part, at the Center for Integrated Nanotechnologies, an Office of Science User Facility operated for the U.S. Department of Energy (DOE) Office of Science.