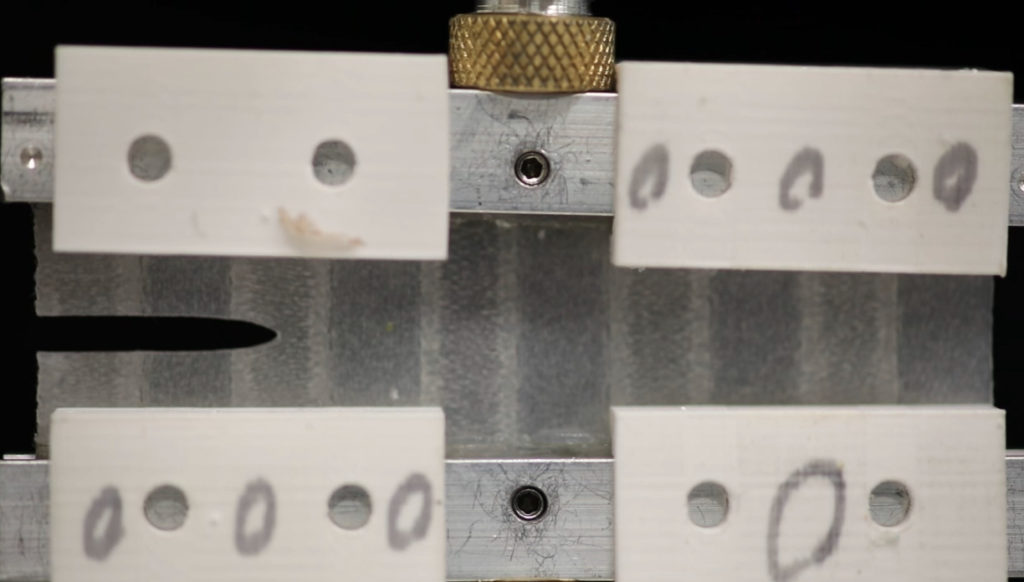
The human heart beats more than two billion times in an average lifespan. The aorta’s tissue is strong enough to withstand this stress, yet flexible enough to maintain a steady flow of blood. But how does this soft tissue not tear over time? This is a question that engineers are trying to answer as they examine the physical properties of soft materials, such as silicones or hydrogels, which are commonly used in robotics, medical devices and wearable technologies.
In the engineering world, traditional soft materials are either tough, meaning difficult to tear, or stiff, meaning able to resist deformation. The tradeoffs that come with each of these properties make it challenging to design a material that is both. Previous approaches involve combining two types of materials, alternating the placement of rigid and flexible materials throughout a final composite material to help prevent and slow tears. However, manufacturing a product made from multiple material types increases the cost and slows production time, as it requires investment in creating chemical compatibility between the two materials to allow them to stick together.
To tackle the issue of making soft materials tough, Penn Engineers have examined the problem from a different angle — literally, the angle at which glass fibers embedded in silicone come out of a 3D-printing nozzle.
Taking solutions from nature, Jordan Raney, Assistant Professor in Mechanical Engineering and Applied Mechanics, along with Chengyang Mo and Haiyi Long, graduate students in his lab, looked at the variations of fiber alignment in biological tissues to find an answer in their new study published in PNAS.
“The answer to many problems in nature is spatial variation,” says Raney. “Tissues are made up of features with varying patterns and degrees of order, and this heterogeneity of the structure allows it to perform multiple functions simultaneously. In engineering soft materials, you can either create heterogeneity by employing multiple material types or by changing a few aspects of one type of material, such as fiber alignment. Our approach is the latter.”
The researchers mimicked this variation by manipulating one type of silicone, polydimethylsiloxane. They embedded glass fibers into this soft silicone to provide it with structural fibers akin to collagen in skin. The alignment of the fibers is the key to creating a material that is both tough and stiff, and printing the material with a 3D printer allows the researchers to manipulate both the print path and the nozzle rotation to change the alignment of the glass fibers and tune the material for various needs. This design moves away from using two separate plastic materials to achieve the desired mechanical properties, and instead employs variations of fiber alignment to provide toughness.
“As the material comes out of the nozzle, the glass fibers align,” says Raney. “This means we can manipulate the alignment of the fibers by simply changing the print path. We then tested two different patterns of fiber alignment to examine the effect on toughness and stiffness.”
The first pattern was a striated soft material where each stripe contained glass fibers that were either parallel with or perpendicular to the direction of the tear.
“Here we created a simple tear-resistant material by just manipulating the fiber alignment,” says Mo, the study’s lead author. “We were able to slow the tear and we can easily manipulate the number of stripes to attune the material to different applications where it might need flexibility over toughness or vice versa. But we didn’t stop there. We wanted to improve these properties further, and that’s when we looked at the aorta.”
The aorta is made up of three layers where the top and bottom layers’ fiber alignments are highly heterogeneous compared to the middle layer, which has relatively homogenous alignment. The variation of fiber alignment across these three layers allows the tissue to be both tough and stiff.
“We were able to mimic the aorta tissue in our soft material by employing a rotating 3D printing nozzle that created helical glass fiber alignments in the top and bottom layers,” says Mo. “We created the middle layer by manipulating the print path of a non-rotating nozzle resulting in highly aligned fibers. Together, the three layers were able to resist and slow tears to a higher degree than our first material.”
“The aim of this study was to combine properties of materials to create something new and applicable across many fields,” says Raney. “It has been often pointed out that, with 3D printing, complexity comes for free. With traditional methods of manufacturing, such as creating molds and casts, we can’t easily control the internal features of a material, like fiber alignment. But with 3D printing we can.”
It is the complicated, spatially varying fiber alignment that aids in the structural integrity of the soft material.
“We chose glass because it is cheap and widely available,” says Mo. “But it’s not the glass that is important here, it’s the alignment, the geometric pattern, that creates the toughness we are looking for. This design, based upon theoretical research, can be applied using other types of materials in place of glass and still achieve the desired properties, making it even more accessible and efficient.”
Since the researchers have successfully demonstrated this theory through experimentation, they are already diving into follow-up studies.
“Some of our immediate next steps in this research are improving the material by manipulating its chemistry,” says Mo. “Additionally, we made the aorta-inspired tissue tougher than it is stretchable so we will be finding new ways to increase its ability to stretch for applications such as wearable devices that integrate with the human body.”
“As we move into future research projects with this soft material, it is important to understand the fundamentals of these properties and that when you change one, it influences another,” says Raney. “Before we delve into the real-world applications of this material, we have to understand it on this fundamental level, and fortunately for us, we are very excited to be studying the fundamentals.”
Flexible and tough soft materials have a wide range of applications and those such as soft robotics, biomedical devices and wearable tech are only a few. Materials that mimic skin and tissue will likely solve problems in many fields and open doors to new technologies and biomimicry research approaches along the way.