Incubating Innovation
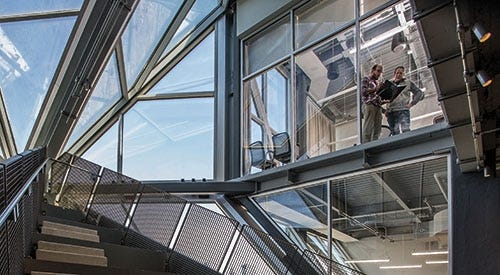
When Matt Lisle (BSE’15) started his freshman year at Penn, most of the upperclassmen he knew were looking into banking or consulting jobs, and none were starting companies. “By my senior year, that ratio had almost completely flipped,” he says. What brought about the change? According to Lisle, it was the product of Penn’s initiatives designed to inspire budding entrepreneurs. As a result, startups among alumni are finding both great support and success.
Penn President Amy Gutmann has named innovation as one of the three main thrusts of her Penn Compact 2020. In 2014, she introduced the President’s Engagement Prizes, which empower Penn seniors to design and undertake local, national or global projects during the first year after they graduate. One year later, Gutmann announced the launch of the President’s Innovation Prize, which provides social-minded graduating seniors with financial support and mentorship during the first year out of college, in addition to dedicated space at the recently opened Pennovation Center.
One notable example of Penn’s commitment to entrepreneurship is the Y-Prize, which was launched in 2012 by Vijay Kumar, Nemirovsky Family Dean of Penn Engineering, and Mark Yim, professor in Mechanical Engineering and Applied Mechanics (MEAM) and director of the Integrated Product Design master’s degree program. This award provides $10,000 to members of the Penn community who propose the best application for an emerging technology.
Penn Engineering students can also take advantage of opportunities such as the PennApps and Pennvention competitions, the Engineering Entrepreneurship Program, and the I-Corps Site summer startup accelerator program, among others. That’s not to mention strong collaborations across Engineering, Wharton and Medicine at Penn, access to outstanding mentors and a broad network of alumni, the extensive hands-on curriculum, and the growing number of cutting edge technologies available to students.
As showcased by the four projects that follow, the innovation community at Penn is flourishing. “Penn Engineering is positioning itself to unleash the next generation of high-tech entrepreneurs,” says Adrian Lievano (BSE’15). “It’s a natural place for any aspiring entrepreneur to make their bold ideas come true.”
Meeting The World’s Water Needs
With the help of a 2015 President’s Engagement Prize, Lisle and Lievano (pictured top row, middle) are tackling one of the biggest challenges of the 21st century: meeting the world’s growing water needs in the face of a changing climate. The award allowed the duo to spend the 2015–16 academic year designing and implementing a simple, sustainable and inexpensive water filtration system in Kimana, Kenya, where access to clean drinking water is a daily struggle.
Upon graduation, Lisle and Lievano launched the startup Everwaters to develop their system. The result of their efforts was a water filter made of coconut carbon and natural ceramic, which work together to reduce lead, bacteria and rotavirus, the most common cause of severe diarrheal disease in infants and young children worldwide.
The product removes more than 15 times the number of contaminants as a Brita filter, and was the focus of a Kickstarter campaign initiated in November 2016. Thousands of filters are now en route to Kenya, and Everwaters also plans to expand in East Africa and other developing and emerging markets.
Lisle and Lievano are also developing a filter that leverages the natural water purification capabilities of the moringa seed, which contains a coagulant protein that binds heavy metals and microorganisms, effectively removing them from the water. In the end, the filters could save countless lives from waterborne diseases and metal poisoning. “We think we can start and grow a sustainable, socially responsible business,” Lisle says. “Looking back, becoming an entrepreneur was the most fulfilling direction to take, and I’m grateful that both the people and my experience at Penn showed me the way.”
Made-To-Order Organs
Danny Cabrera (BSE’14) did not spend his weekends like a typical college student. Instead, he and Ricardo Solorzano (BSE’13) holed up in an apartment located above a noisy college bar, and toiled on a Frankenstein-like device that extruded a 3D matrix of living tissue. Once they were satisfied with their creation, Solorzano suggested that they enter it into the 2014 Pennvention investor’s competition.
The idea paid off. The duo’s team, BioBots, won the $5,000 grand prize for a 3D printer that can sculpt cell cultures into miniature organs. Like an inkjet printer, 3D printers have a moving nozzle that translates a digital pattern from a computer into a physical object. But instead of using ink, the BioBots printer uses a solution of biomaterials.
Containing living, growing cells and vasculature to feed them, the 3D constructs can serve as model organs for drug testing and other types of biomedical experiments, offering a humane alternative to animal-based research. In the future, the technology may advance to a stage where fully functional artificial organs could be made to order from a patient’s own cells. This breakthrough would hold promise for eliminating the organ waiting list and reducing the risk of harmful immune responses that cause transplant rejection.
At their startup company BioBots, Cabrera (pictured above) and Solorzano are already working on a second-generation version of their printer, and hundreds of scientists in more than 20 different countries are currently using their products. “I am constantly inspired by our partners’ research projects, goals and progress,” Cabrera says. “They remind me that we are accelerating the pace not only of regenerative medicine, but of human evolution.”
Robots To The Rescue
Imagine hundreds of small flying robots swarming over the site of an airplane crash, searching across thousands of square miles for human remains amidst the debris- and tree-filled landscape. Or a team of robotic weather balloons that can hover low in the atmosphere to monitor man-made and natural disasters, such as gas leaks, fires or nuclear meltdowns. These scenarios may have come a step closer to reality with the introduction of Piccolissimo, the world’s smallest self-powered controllable flying vehicle.
Italian for “tiniest,” Piccolissimo is the brainchild of Matt Piccoli, a doctoral student in Mark Yim’s Modular Robotics Lab (ModLab). The smaller version of the robot weighs less than 2.5 grams and is about the width of a quarter. Yet it is big enough to carry a camera or sensor, and when deployed in the hundreds or thousands, can quickly gather data over a large area for applications such as search and rescue, disaster relief and agriculture.
The idea for this project only came to fruition because of the unique, cutting-edge equipment and facilities of ModLab, part of the General Robotics, Automation, Sensing and Perception (GRASP) Laboratory, in addition to MEAM’s AddLab, Precision Machining Lab, and the Rapid Prototyping Lab, Piccoli says.
“I also benefited from Penn’s wide range of expertise by taking classes in Mechanical and Electrical Engineering and Computer Science, and in Integrated Product Design as an upperclassman and a graduate student,” he says. “These courses not only helped me perform my research, but also taught me how to make a well-rounded product.”
Wielding Water In Workshops
For Nisan Lerea (BSE’12), a major part of the Penn experience was racing. Along with other members of the Formula SAE team, he designed, fabricated and competed against other schools with small formula-style race cars. He did almost all of the custom metal fabrication in-house, spending hundreds of hours cutting and shaping sheet metal with hand tools.
A solution to decreasing the amount of time spent on metal fabrication arose through his MEAM Senior Design project. With the help of several classmates, Lerea developed WAZER: the first small-scale, low-cost waterjet for Penn Engineering. A few years after graduating, Lerea (above right) and fellow racer Matt Nowicki (BSE’10, above left) quit their jobs to turn the project into a business.
WAZER uses an ultra-high pressure stream of water containing abrasive particles capable of eroding through the toughest materials. The consumer-friendly tabletop tool can cut virtually any material with digital precision, enabling individuals to convert their ideas into finished goods themselves. Applications range from developing drone prototypes, manufacturing signs, and even crafting glass artwork, ceramic pottery and stone sculptures.
“Once we get the initial machines out into the world, we’ll be able to learn from our users what’s most important to them,” Lerea says. “We’ve created a unique tool that enables creativity and independence, and we can’t wait to see what people make with it!”