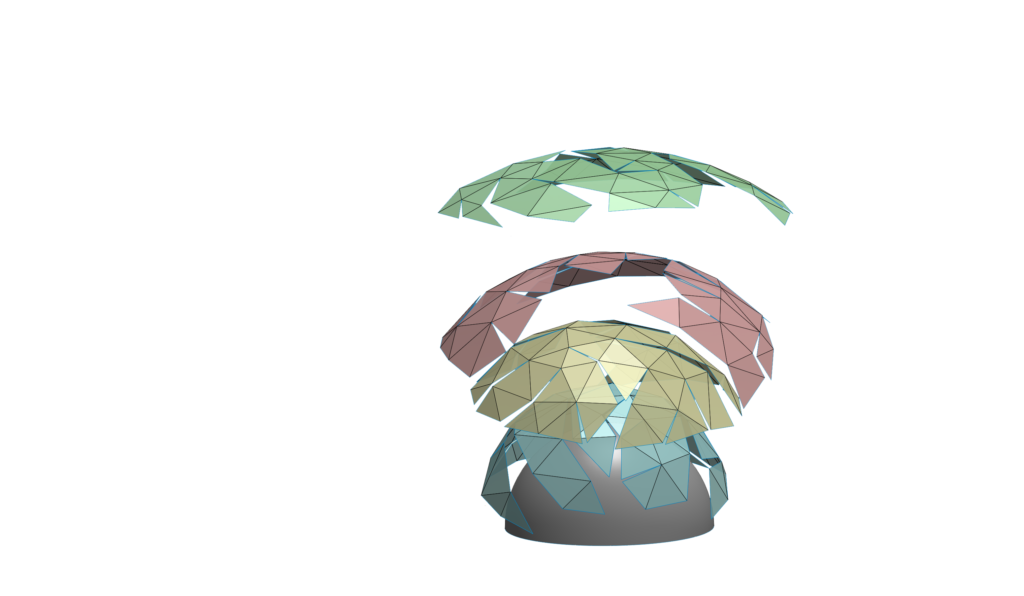
Penn researchers have developed a universal algorithm that allows 2D materials to retain mechanical strength after conversion into 3D structures.
The algorithm is the subject of a recent study in Science Advances led by Shu Yang, Joseph Bordogna Professor and Chair of the Department of Materials Science and Engineering (MSE), along with MSE postdoctoral fellows Lishuai Jin and Young-Joo Lee and collaborators Michael Yeager and Daniel J. O’Brien of the DEVCOM Army Research Laboratory.
The team’s work takes inspiration from kirigami, an East Asian papercutting art, to create a mathematically sound method of cutting and stacking flat materials into durable curved objects.
The advance addresses a longstanding blind spot at the intersection of mechanical engineering and materials science: Hardwearing materials with high mechanical integrity lose strength when manipulated into three-dimensional (3D) forms. Yet this loss is rarely quantified or questioned, even when these materials are selected for protective or loadbearing applications.
“Once you introduce cuts,” says Jin, “the material is always weaker. Surprisingly, in protective applications, engineers have prioritized shape and fit over mechanical properties. They assume high-strength materials remain high-strength materials even after slicing out darts to avoid wrinkling or cutting and layering to line a mold. But every cut is a defect that compromises the mechanical properties of a material, and this is exactly what our algorithm resolves.”
Materials manufacturing favors two-dimensional (2D) forms for easy fabrication. The necessity of 2D-to-3D transformation presents challenges. Cuts are necessary to avoid wrinkles and overfolds in the final 3D curved objects. In other words, material-weakening defects are unavoidable.
Kirigami art is compelling for this reason. It allows for flexibility of form through discontinuity, pursuing defect to afford dimension.
Penn engineers embraced kirigami with the knowledge that mechanical strength lies not in the nature of defects, but the defects of nature.
The team’s approach looks beyond existing engineering processes to capitalize on recent research on the robust mechanical properties of mollusks. Their algorithm allows hard materials to retain their strength after cutting by mimicking the structure of nacre, the iridescent natural shell coating known as mother of pearl.
For any shape, the algorithm can create a computational map of cuts optimized for stacking. It compensates for the necessary defects by guaranteeing these cuts never overlap with one another. It further reinforces the mechanical strength of the resulting 3D object with the addition of fortifying tabs.
“Materials scientists think about structure at many different scales,” says Yang. “Working together with mechanical engineers, we translate insights from nature at the nanoscale into a design that is completely scale independent. This algorithm provides a geometry that is as useful for objects measured in microns as it is for those measured in meters. Helmets, protective face masks, architectural support structures, airplane parts—all you need is the algorithm to optimize the cutting and layering so the material strength is intentionally maintained rather than assumed and lost.”
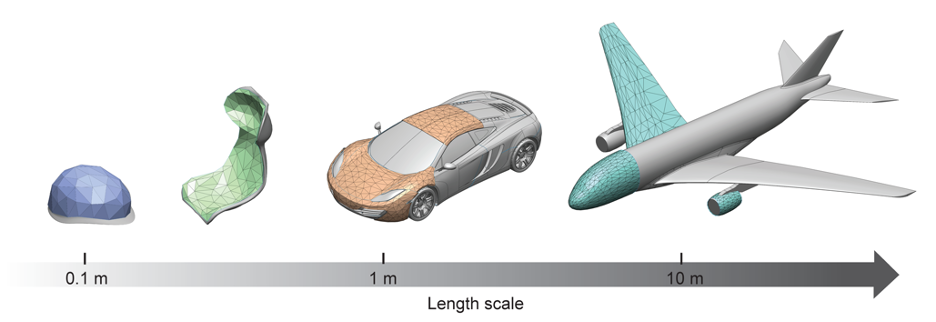
The algorithm also functions as a design guide for effective material use. Because each cut diminishes material strength, edges and trim must be eliminated or minimized. This strength-minded approach doubles as a waste-reducing feature.
Yang’s lab and her collaborators are exploring a variety of applications for kirigami structures: building envelopes for energy efficiency, water harvesters to address resource shortages and reconstructive surgery techniques to reduce costs and improve patient outcomes.
“The algorithm can generate efficient and intelligent cut patterns no matter the size. It optimizes for strength as well as material usage and is perfect for irregular or organic geometries,” says Yang. “We developed it for real-life applications, where structures are rarely if ever generalized or symmetrical. This is the case for bodies as well as the built world—the algorithm is infrastructural in every sense of the word.”
This research is supported by the U.S. Combat Capabilities Development Command (DEVCOM) Army Research Office (ARO), ARO no. W911-NF-1810327.