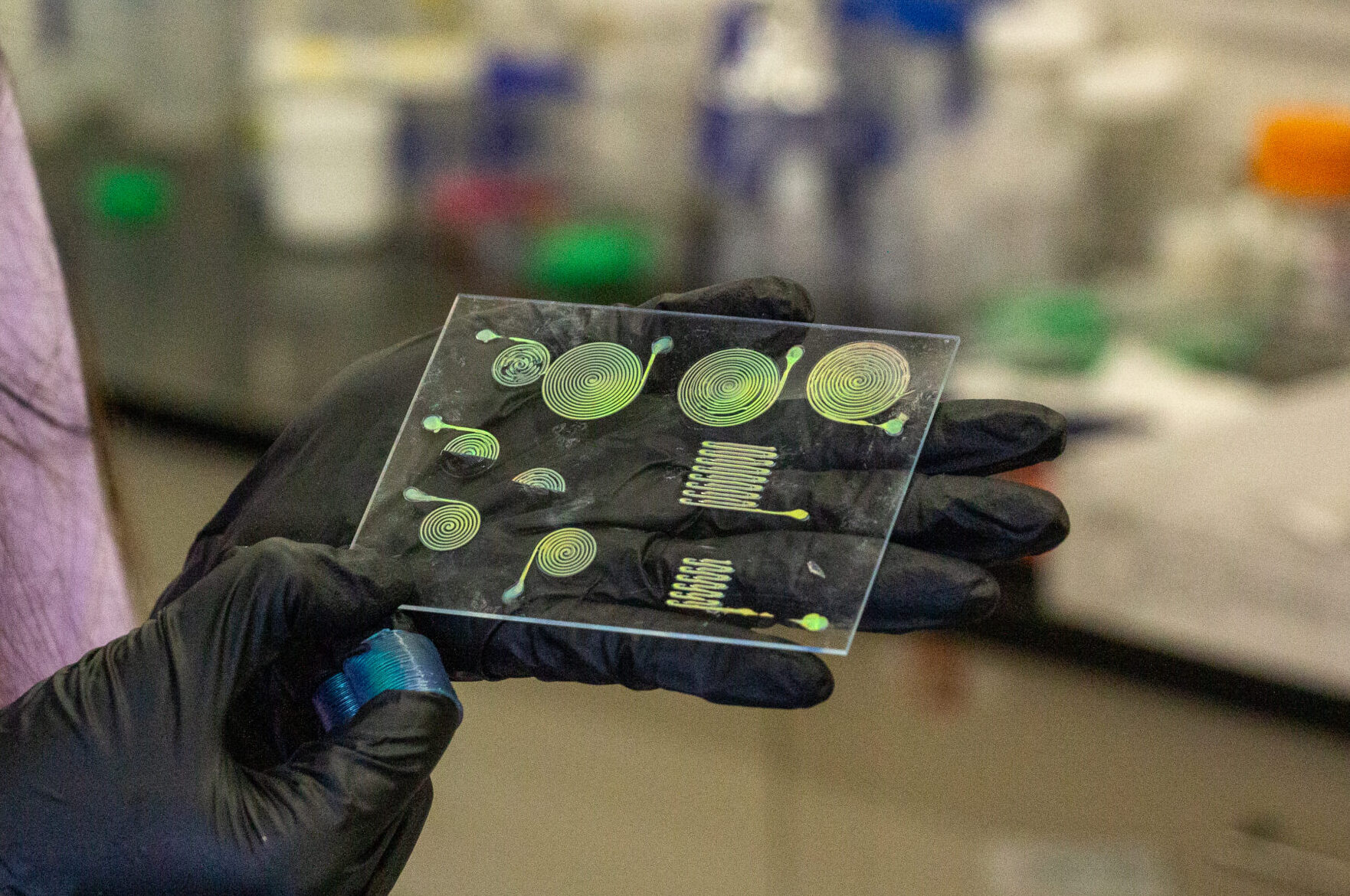
In a breakthrough that promises to reshape the future of smart materials, a multidisciplinary team of researchers from Penn Engineering, Harvard University, Duke University,* University of California Berkeley* and Lawrence Livermore National Laboratory (LLNL) have successfully developed a cutting-edge method to 3D print cholesteric liquid crystal elastomers (CLCEs), opening the door to dynamic, color-changing materials that can respond to mechanical stress. This innovative work, published in Advanced Materials, combines advanced printing techniques with unique material properties to pave the way for groundbreaking applications in smart sensing, displays, robotics and beyond.
At the heart of this advancement are CLCEs — soft, rubbery materials capable of changing color when subjected to mechanical stress.
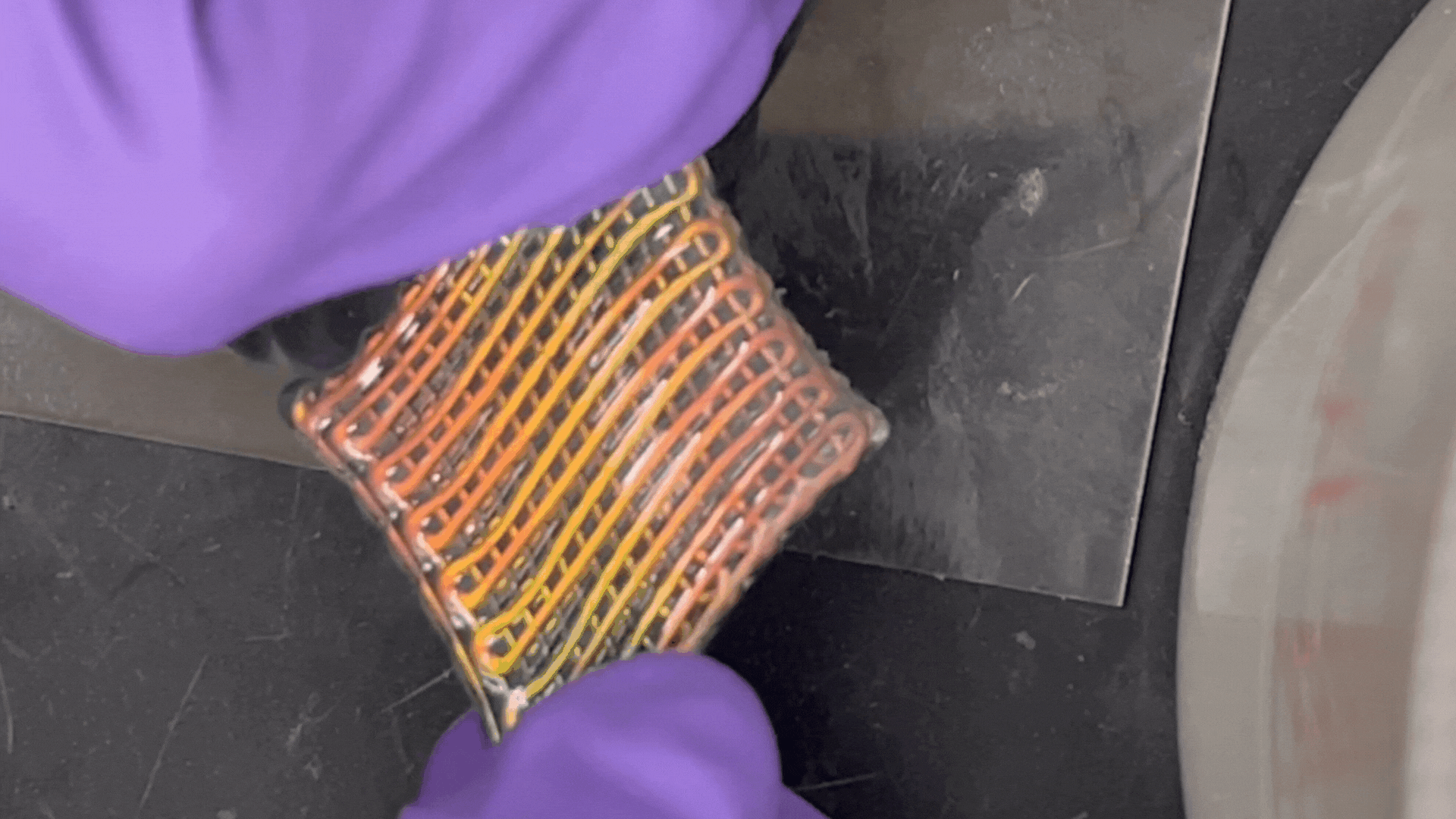
“The color changes are caused by the material’s ability to manipulate light, much like a beetle shell reflects light to create a colorful display,” says Shu Yang, Joseph Bordogna Professor and Chair of Materials Science and Engineering (MSE) and lead investigator of the work. “These materials have the potential to solve industry problems across medicine, diagnostics, monitoring and can even be used in art. My lab is working with these responsive materials to discover new ways to observe and interact with the world around us.”
Breaking New Ground with 3D Printing
Traditionally, CLCEs have been limited to 2D planar films, like those in liquid crystal display (LCD) TV screens and monitors. Bringing these light-interactive materials into the third dimension would open doors for more applications. The team’s innovation centers around a novel 3D printing technique known as Coaxial Direct Ink Writing (DIW), which allows for the precise printing of multi-stable, color-changing structures.
“It’s gratifying to see Coaxial DIW, a method that we co-developed with researchers at LLNL more than a decade ago, being applied to CLCEs”, says Jennifer Lewis, Wyss Professor of Biologically Inspired Engineering at the Paulson School of Engineering and Applied Sciences and the Wyss Institute at Harvard University and Director of Harvard’s Materials Research Science and Engineering Center (MRSEC).
However, when turning 2D structures into 3D structures, things get a little complicated. In this case, the liquid precursor of the CLCE is so viscous, that when pushed through a 3D-printing nozzle, it hinders the formation of the twisted helix structures which are responsible for the color-changing characteristics of the CLCEs.
To solve this problem, Alicia Ng, Ph.D. student in MSE and lead author of the study, and her colleagues set out to find the perfect CLCE viscosity: thick enough to maintain the structural integrity of the finished product but not too thick to allow the material to easily flow through a printing nozzle. The key ingredient that optimized the process was a completely different material, silicone, which was a game changer in their innovative technique.
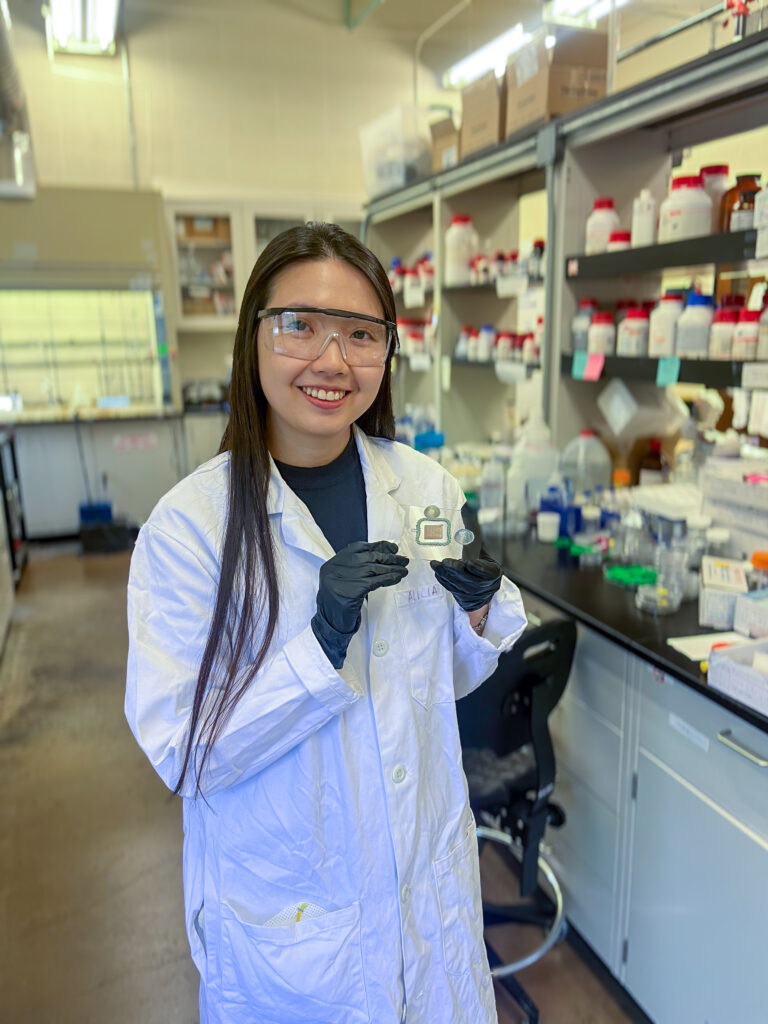
“We developed a transparent silicone shell to serve as a scaffold for the CLCE core,” says Ng. “This unique combination of materials allowed us to preserve the color-changing properties of the CLCEs while providing the necessary structural strength to support intricate 3D designs.”
A Leap for Smart Materials and Wearables
The potential applications of this technology are vast and varied.
“We envision using these materials to create devices that give real-time, visual feedback, whether it’s in a wearable form or embedded in a larger structure,” says Yang. “This could allow us to observe mechanical stress in a way that was previously impossible with traditional materials.”
Beyond healthcare, for example a smart wrap that indicates when a joint or part of the body swells, the team is exploring how these color-changing materials can be incorporated into various systems that respond to environmental changes, from robotics to interactive art and environmental sensors.
“For example, robotic grippers that can snap open and closed, metamaterial sheets that can passively sense and record mechanical loads, and mechanical logic systems that can compute without conventional electronics are just a few areas where CLCEs can contribute to new technologies,” says Katherine Riley, mechanical engineer at LLNL.
The Road Ahead: Beyond Color-Changing Materials
Looking to the future, the research team is exploring ways to combine CLCEs with temperature- or light-responsive materials to create materials that change color in response to a variety of stimuli. They also are looking to nature to make these materials more eco-friendly.
“We may look into incorporating elements from biofilms,” says Yang. “That could allow us to create self-building, regenerative structural colors that are both environmentally friendly and functional.”
In terms of design, the team has already printed various structures, including lattices, wraps and filaments, and they are eager to explore even more complex designs. With the ability to print directly onto curved surfaces, such as body parts, the team envisions wearable devices that seamlessly conform to a user’s shape.
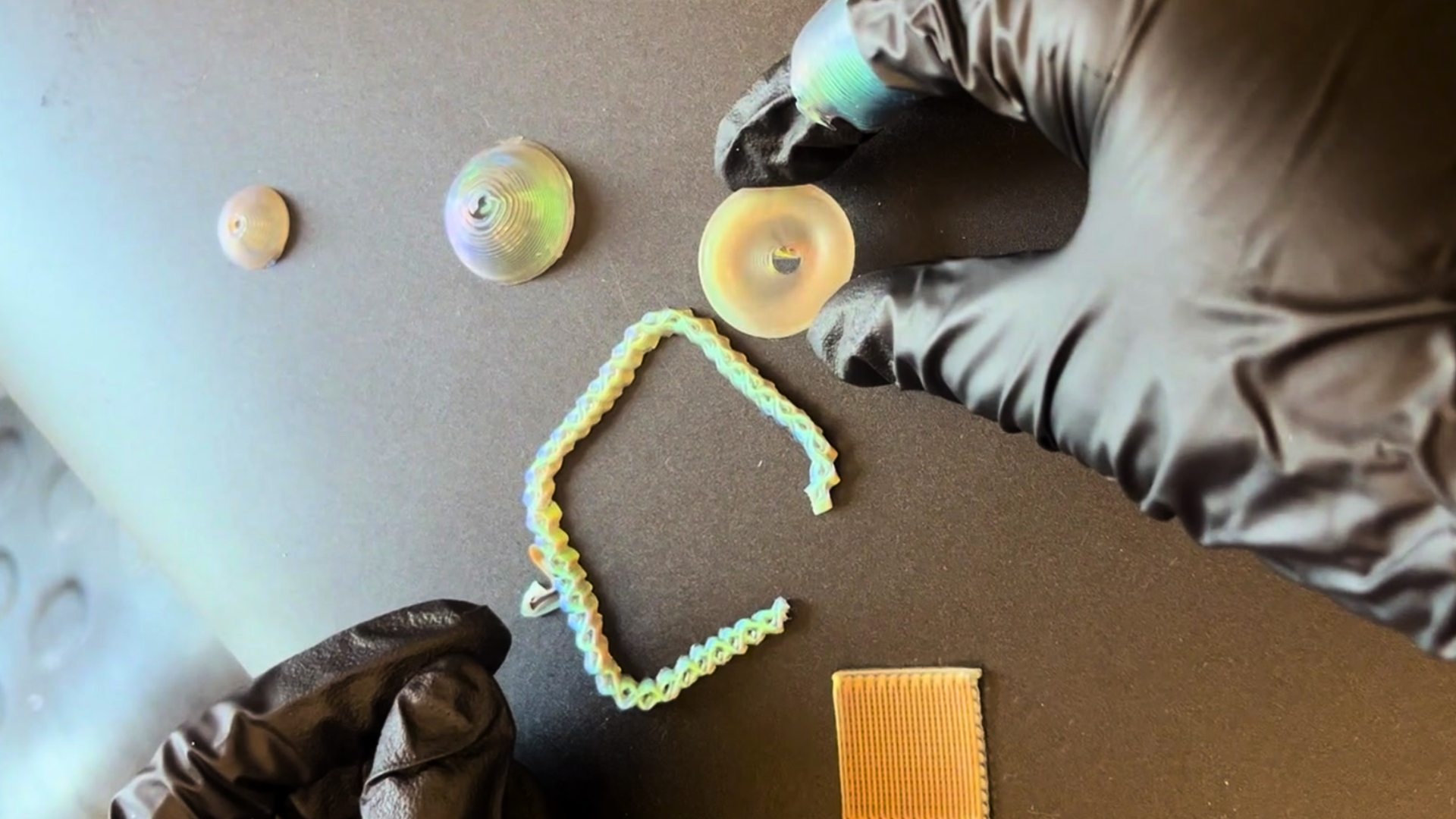
“Looking ahead, we are expanding upon this research through an LLNL Laboratory Directed Research and Development Strategic Initiative (LDRD SI) aimed at combining the design and fabrication of complex architectures with automated materials training to develop ‘sentient’ materials,” says Elaine Lee (MSE’15), LLNL engineer and Penn Engineering alumna.
“These CLCE materials could play a crucial role in rapidly iterating new designs via remote detection paired with automated on-machine metrology techniques such as digital image correlation,” adds Caitlyn Cook Krikorian, Functional Architected Materials Engineering (FAME) group leader and deputy director for the Center of Engineered Materials and Manufacturing (CEMM) at LLNL.
Mentorship and collaboration support the next generation of engineers
The team’s approach to fine-tuning this DIW process comes from their combined experience in polymers, liquid crystal elastomers (LCEs) and 3D printing, and Ng’s multiple internships with LLNL allowed her to bridge the various expertise of each group.
“This project was successful only because I had such strong support through the collaboration between Penn and LLNL,” says Ng. “Every summer since I started my Ph.D. at Penn Engineering, I worked with the LLNL on various LCE projects, and Elaine and Caitlyn brought me in and nurtured me as if I were their own student. There, I also worked with Professor Jennifer Lewis and Rodrigo Telles, who taught me how to utilize the custom-built DIW printer at LLNL and shared with me tips and tricks he accumulated from his printing experience. I brought that knowledge back to Penn and I aspire to continue working in this field.”
This research was supported by the National Science Foundation through the DMR/POL program (# DMR-2104841, to S.Y.), Harvard MRSEC (DMR-2011754, to J.A.L.), and the Army Research Office MURI program (W911NF-22-1-0219, to J.A.L.). This work was performed under the auspices of the US Department of Energy by Lawrence Livermore National Laboratory under contract DE-AC52-07NA27344, LDRD tracking number 22-ERD-030 and 25-SI-005, and release number LLNL-JRNL-870063. *Team members from Duke University and the University of California Berkeley are a part of a larger collaborative effort between Penn, the LLNL and Harvard that goes beyond the CLCE work mentioned in this story.